Technical Information
Energy harvesting from ambient vibrations has been in the spotlight recently. The technology is useful for wireless sensor network in automobile where vibration from engine and road is available for power supply for sensors and electronics. Power generation from vibrations is also beneficial in heath monitoring system for bridge and factory, where battery replacement of the device placed in the structure or machinery is troublesome. The technology will also realize battery-free remote controllers for home automation and public welfare if part of kinetic energy of human motion, e.g., pushing bottom, can be converted to electrical energy through vibration.
Vibrational energy harvesting technologies are divided into piezoelectric materials and moving magnet (electromagnetic induction). However, there are few commercial products being used effectively due to their low power generation, low efficiency, and poor environmental endurance. Piezoelectric materials are brittle with poor robustness against bending, tension and impact. They also suffer from the high output impedance by which small amounts of output energy transferred to external loads, even though the generating voltage is high. In moving-magnet type, poor coupling and low resonant frequency are disadvantages for power generation.
We propose novel vibration based energy harvesting technology using an iron based magnetostrictive material, Galfenol, with good machinability, high robustness and high coupling coefficient. The principle is based on force conversion mechanism using parallel beam structure and large inverse magnetostrictive effect of Galfenol, where the magnetization can be varied more than 1T by a mechanical stress.
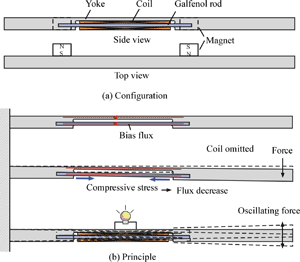
Configuration and Principle
The device consists of single Galfenol rod (Fe81.6Ga18.4), coil, permanent magnet and magnetic yoke. The rod with magnetically easy axis in longitudinal direction is stress-annealed under a compressive stress to yield flux changes both by compressive and tensile stress. The rod is parallel with the yoke with appropriate interval for winding coil and its ends are strongly fixed on the yoke for force transduction. The permanent magnets attached on the yoke provide bias flux for the rod.
The bending deformation of the device generates a voltage on the coil. For example, we assume that one end of the device is fixed like cantilever. When a force is exerted downward on the edge, the rod is subjected to compressive force in the longitudinal direction in bending deformation. The compressive stress causes a flux decrease due to the inverse magnetostrictive effect. On the contrary, an upward force causes tensile stress and a flux increase in the rod. Consequently, time variation of the flux caused by oscillating force though vibration generates a voltage on the coil by Faraday's law of induction.
The parallel beams structure functions as force amplification mechanism which converts small bending force to large axial force on Galfenol rod. The induced axial stress is large and one directional in most part in the rod, for which bending force much smaller than axial force (1/20) is necessary for same stress. In addition, the device consists of iron based materials, Galfenol and yoke, is simple and rigid which also contributes on high resonant frequency and low mechanical loss. Therefore, the mechanical energy is converted efficiently to electrical energy due to the high coupling coefficient of Galfenol (> 0.7), and the output power proportional to the frequency and exciting force of vibration source is high due to the high resonance and high durability. (Output power, Watt, is proportional to force multiplied by velocity. The operating frequency providing highest output is resonance.) The electrical energy is also transferred efficiently to the external electrical load because of the low electrical impedance of the coil.
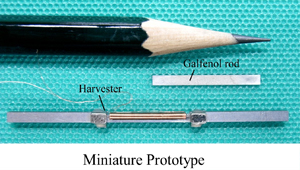
The characteristics were verified by miniature prototype. The Galfenol rod was 2.0 mm width 0.5 mm thickness 16 mm length with a wound coil of 1260 turns (95 W). Four Nd-B-Fe magnets of 2 mm by 3 mm and 1 mm thickness were used for bias. The thickness of the yoke and interval between the rod and yoke in parallel beam were 0.5mm.
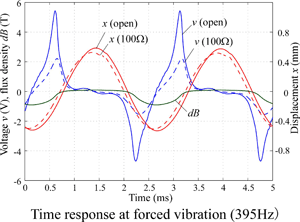
The prototype had 1st bending resonant frequency around 400 Hz. Figure shows the time responses at 395Hz with open and R = 100 W connected. In this measurement, the device was oscillated at maximum vibrational acceleration of 150 m/s2 (15.3 G). The maximum voltage was 5.4 V in open at the amplitude x of 0.6 mm. The voltage generation is the result of time variation of flux density dB with the width of 1T. With resistance of R=100 W, the maximum voltage was 2.2V, where the maximum power of 48mW was obtained. The displacement with R is smaller than that of open due to the damping effect accompanied by the energy conversion of the mechanical to electrical energy (Joule loss).
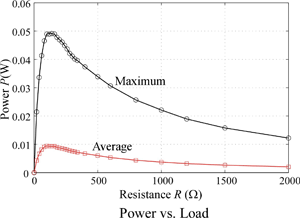
The relationship between R and power of the maximum Pmax and average Pavgcalculated by average of time integration of v2/R is shown. The maximum of Pmaxand Pavgwere 50 mW and 10mW (power density 40 mW/cm3) respectively at impedance matching condition around R = 100 W close to the value of the resistance of the coil. These results demonstrate high output power can be extracted at low impedance load such as LED and supper capacitor where output energy is consumed and charged efficiently.
Publication
- T. Ueno, S. Yamada, "Performance of Energy Harvester Using Iron Gallium Alloy in Free Vibration",IEEE TRANSACTIONS ON MAGNETICS,Vol. 47,10,pp. 2407 - 2409, (2011).